In the world of electrical engineering, porcelain insulators have carved out a niche that speaks not only to their functionality but also to their beauty and resilience. These often-overlooked components play a crucial role in supporting overhead power lines and ensuring safe transmission of electricity. Made from a mixture of clay, feldspar, and quartz, porcelain insulators are meticulously crafted to withstand the harshest of environments while providing an aesthetic touch that many appreciate.
The enduring legacy of porcelain insulators is evident in their widespread use, dating back over a century. Their ability to resist moisture, pollution, and extreme weather conditions makes them indispensable in both urban and rural settings. Beyond their practical applications, these insulators have also become collectible items for enthusiasts, celebrated for their unique designs and historical significance. As we delve deeper into the world of porcelain insulators, we uncover a fascinating blend of art and engineering that continues to captivate us today.
History of Porcelain Insulators
The use of porcelain as an insulator material dates back to the late 19th century, coinciding with the rapid development of electrical infrastructure. While the discovery of porcelain itself occurred much earlier in history, its application in electrical insulators emerged when the need for reliable components to support and protect electrical wires became essential. Early adopters recognized the advantages of porcelain, particularly its ability to withstand high voltage and environmental elements, paving the way for its widespread use in the industry.
As electrical systems expanded across cities and rural areas, the design and manufacturing of porcelain insulators evolved. Initially crafted by skilled artisans, these insulators began to be produced in factories, capitalizing on advancements in industrial processes. Companies developed various designs tailored for specific applications, including suspension insulators for overhead power lines and pin insulators for utility poles. This innovation led to an increase in efficiency and reliability within electrical transmission networks, contributing to the growth of the electrical age.
The 20th century saw porcelain insulators reach new heights in both design complexity and production scale. With the rise of high voltage transmission lines, engineers and manufacturers focused on enhancing the performance characteristics of porcelain insulators to ensure longevity and reliability. Despite the advent of alternative materials, such as fiberglass and composite insulators, porcelain remains a staple in the industry due to its durability and aesthetic appeal. Today, porcelain insulators hold a significant place in historical and contemporary electrical systems, symbolizing the enduring legacy of engineering and craftsmanship.
Manufacturing Process
The manufacturing of porcelain insulators begins with the careful selection and preparation of raw materials. The primary components include kaolin clay, feldspar, and quartz. These materials are thoroughly mixed in specific ratios to achieve the desired properties such as strength, electrical insulation, and resistance to environmental factors. Once the mixture is prepared, it is processed into a plastic form, allowing it to be shaped into the preliminary design of the insulator.
Next, the shaped insulators are subjected to drying to remove excess moisture. This step is critical as it helps prevent cracking during the subsequent firing process. The drying can be done naturally or in controlled environments, ensuring uniform moisture content throughout the insulator. After drying, the insulators undergo a firing process in a high-temperature kiln, which can reach temperatures of up to 1400 degrees Celsius. This firing transforms the raw materials into a dense and durable porcelain product.
Once the insulators are fired and cooled, they are inspected for quality and consistency. Any defects identified during this stage can result in the rejection of the insulator, ensuring that only the highest quality products reach the market. After passing quality checks, the insulators are often coated with a waterproof glaze, enhancing their resistance to environmental elements. Electrical porcelain insulator are then packaged and prepared for distribution, showcasing the fusion of craftsmanship and technology in the art of porcelain insulator manufacturing.
Types of Porcelain Insulators
Porcelain insulators come in various forms, each designed for specific applications in electrical and telecommunications systems. The most common types include pin insulators, suspension insulators, and strain insulators. Pin insulators are typically used for lower voltage applications and are mounted on poles with a pin that secures them in place. Their design allows for flexibility and easy installation, making them a popular choice for distributing electrical power across distances.
Suspension insulators are designed to support high voltage transmission lines. They are usually arranged in a series, hanging from a supporting structure to provide insulation and mechanical strength. Their shape and construction enable them to withstand extreme weather conditions and maintain stability while supporting the weight of the conductor. This type of insulator is vital for ensuring the safety and reliability of electrical grids.
Strain insulators, on the other hand, are used in situations where tension is present, such as at the ends of transmission lines or when changing the direction of the lines. These insulators are built to endure high tensile forces, securing the line while preventing electrical leakage. Their robust design is essential in maintaining the integrity of the system even under challenging conditions, ensuring long-lasting performance and reliability.
Advantages of Porcelain Insulators
One of the primary advantages of porcelain insulators is their exceptional durability. Porcelain, being a ceramic material, exhibits remarkable resistance to harsh environmental conditions, including extreme temperatures, moisture, and ultraviolet radiation. This resilience ensures a long service life, making porcelain insulators a reliable choice for various applications in power distribution and telecommunications. Their ability to withstand physical stress and temperature fluctuations significantly reduces the need for frequent replacements.
Another key benefit of porcelain insulators is their excellent electrical insulating properties. Porcelain is a non-conductive material, which minimizes the risk of electrical leakage and improves overall system efficiency. This characteristic is particularly vital in high-voltage applications, where maintaining electrical integrity is critical. Furthermore, porcelain insulators provide excellent dielectric strength, allowing them to operate effectively even under challenging electrical stresses.
In addition to their functional advantages, porcelain insulators also offer aesthetic appeal. Unlike other materials that may degrade or discolor over time, porcelain maintains its appearance and structural integrity for many years. This quality makes porcelain insulators not only practical but also visually pleasing in both urban and rural settings. The combination of durability, functionality, and beauty reinforces porcelain insulators as a preferred choice among engineers and designers alike.
Environmental Impact
Porcelain insulators play a significant role in electrical infrastructure, mainly due to their durability and longevity. Unlike many materials used in insulation, porcelain is made from natural substances like clay, feldspar, and quartz. This composition means that its production has a relatively low environmental footprint in terms of resource extraction. Additionally, porcelain insulators have a long life span, often exceeding 50 years, which reduces the frequency of replacements and the associated waste.
The manufacturing process of porcelain does involve energy consumption, but advancements in technology have led to more efficient production methods. Manufacturers are now incorporating sustainable practices, such as utilizing recycled materials and minimizing waste during production. Furthermore, porcelain insulators are resistant to harsh environmental conditions, which allows them to maintain their performance without the need for frequent maintenance or replacement, thus contributing to a reduction in overall environmental impact.
Finally, when it comes to disposal, porcelain insulators are less harmful compared to other insulating materials that might release toxic chemicals. They can be crushed and repurposed for various applications, such as aggregates in construction. The ability to recycle porcelain insulators highlights their adaptability and further solidifies their role in promoting environmentally friendly practices within the electrical industry.
Applications in the Modern World
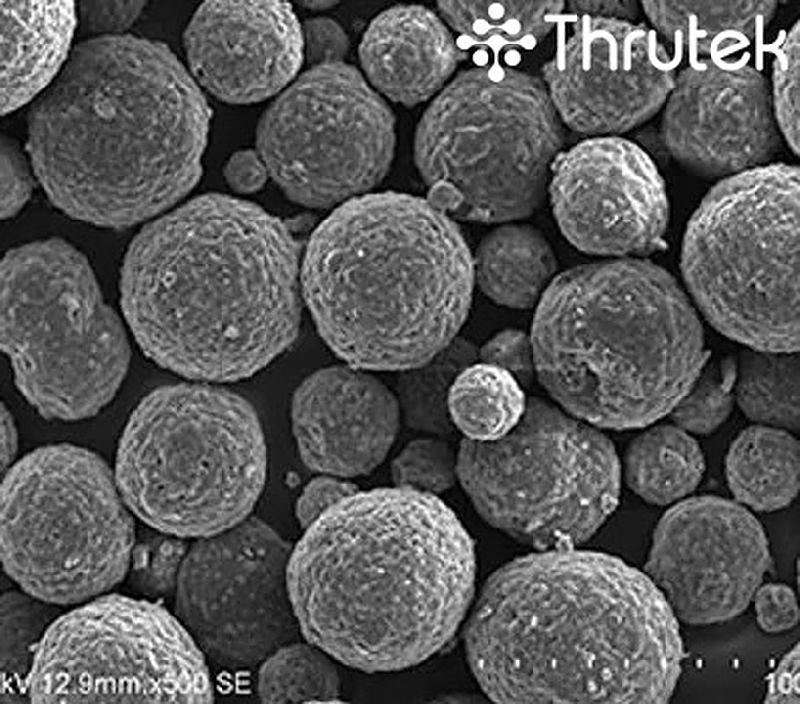
Porcelain insulators continue to play a critical role in modern electrical distribution systems. Their inherent properties, such as high dielectric strength and resistance to environmental factors, make them an ideal choice for power lines and substations. Utility companies rely on these insulators to ensure uninterrupted service and protection from electrical faults, especially in areas subject to harsh weather conditions. The longevity and durability of porcelain insulators contribute to reduced maintenance costs and improved reliability of power transmission networks.
In addition to their use in electrical infrastructure, porcelain insulators have found applications in telecommunications. They are commonly used in telephone and data transmission lines, where minimizing signal degradation is paramount. The ability of porcelain to withstand temperature changes and moisture ensures that communication systems remain operational without interference. This has become increasingly important as global demand for reliable telecommunications grows, further solidifying the place of porcelain insulators in modern technology.
Moreover, porcelain insulators have become a favored choice in renewable energy applications, particularly in wind and solar energy systems. Their non-conductive properties and resilience to the elements make them suitable for protecting equipment and supporting structures in these installations. As the world shifts towards sustainable energy sources, the role of porcelain insulators is likely to expand, demonstrating their versatility and enduring relevance in an evolving energy landscape.
Maintenance and Durability
Porcelain insulators are known for their exceptional durability and resistance to harsh environmental conditions. These insulators can withstand temperature fluctuations, moisture, and UV radiation, which contributes to their long lifespan. Routine inspection is essential to ensure that they remain intact and functional. Any visible damage, such as cracks or chips, can compromise their effectiveness, so addressing these issues promptly is important for maintaining electrical safety.
Cleaning porcelain insulators is a relatively simple process. In areas prone to pollution or heavy debris, a regular cleaning schedule helps preserve their insulating properties. Using a soft brush and a mild detergent solution can remove accumulated dirt and contaminants, ensuring that the insulators operate at optimal performance. It is crucial to avoid abrasive materials that could scratch the surface, which would affect their durability and insulating abilities.
Despite the minimal maintenance required, factors such as age, exposure to harsh chemicals, or extreme weather can impact the longevity of porcelain insulators. Manufacturers typically provide guidelines regarding lifespan and best practices for maintenance. Regular evaluations by qualified professionals not only enhance safety but also contribute to the reliability of power systems relying on these sturdy insulators. Overall, when properly cared for, porcelain insulators offer an enduring and effective solution for electrical distribution.
The Future of Porcelain Insulators
As the demand for reliable electrical infrastructure continues to grow, the future of porcelain insulators looks promising. These durable components have proven their worth in various applications, from telecommunications to high-voltage power lines. With the increasing emphasis on sustainability and longevity in materials, porcelain insulators are positioned to retain their relevance in an evolving market. Their ability to withstand harsh environmental conditions and resist pollution gives them an edge over alternative materials.
Technological advancements are paving the way for innovations in porcelain insulator design and production. Manufacturers are exploring improved glazing techniques and composite materials to enhance performance while reducing production costs. These developments will ensure that porcelain insulators not only meet industry standards but also adapt to the changing needs of utility companies seeking efficient and effective solutions for energy transmission.
Furthermore, the enduring appeal of porcelain insulators extends beyond functionality. There is a growing appreciation for their aesthetic qualities, particularly in collector communities and heritage conservation. As interest in vintage and historically significant materials rises, porcelain insulators may find a unique niche in both modern installations and as artistic elements in various contexts. This dual appreciation for both form and function secures a vibrant future for porcelain insulators in the broader landscape of electrical engineering.